Vakuumprüfgerät (Vakuumprüfung)
Änderungen des Luftdrucks können während des (Luft-)Transports auftreten. Änderungen des Luftdrucks können beispielsweise negative Auswirkungen auf einen versiegelten Beutel oder eine andere luftdichte Verpackung haben. Während eines Lufttransports kann im Laderaum eines Flugzeugs ein Unterdruck entstehen (ausgenommen militärische Flüge).
Zudem kann auch während des Transports in Gebirgsregionen Unterdruck auftreten. Durch diesen Druckunterschied können Schäden an Ihrem Produkt und/oder Ihrer Verpackung entstehen.
Navigieren Sie zu:
→ Testübersicht
→ Maschinenspezifikationen testen
→ Normen und Standards
→ Gründe zum Testen
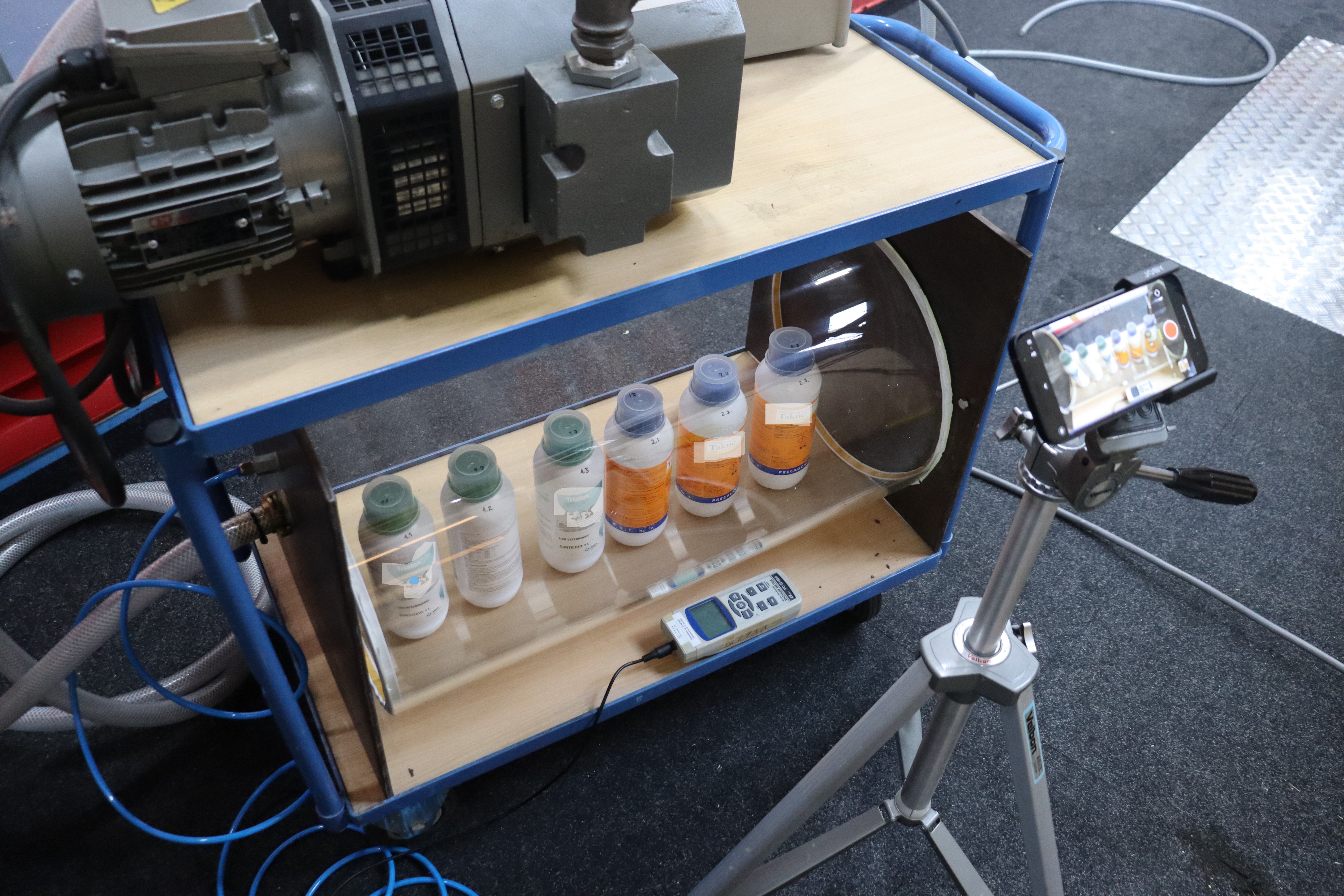
Arten von Vakuumtests
Es gibt verschiedene Arten von Tests, die durchgeführt werden, um Produkte und Verpackungen unter Vakuum- und Druckbedingungen zu bewerten.
Diese Tests hängen von der Anwendung, der Umgebung, in der das Produkt verwendet wird, und den potenziellen Risiken ab, denen das Produkt ausgesetzt sein könnte.
- Leckdetektion: Aufspüren von Lecks in Verpackungen, Gehäusen oder geschlossenen Systemen.
- Berstdrucktests: Bewertung des maximalen Drucks, den eine Verpackung, ein Bauteil oder ein Gehäuse aushalten kann, bevor es versagt.
- Simulation von niedrigem Luftdruck: Simulation von Bedingungen in großer Höhe oder in Raumfahrtumgebungen.
- Feuchtigkeits- und Kondensationskontrolle: Bewertung, wie Produkte auf niedrigen Druck in Kombination mit Feuchtigkeitsansammlung oder Kondensation reagieren.
- Höhentests: Simulation von niedrigen atmosphärischen Drücken in großen Höhen (z. B. in Flugzeugen oder Gebirgsregionen).
- Thermischer Zyklus mit Druck: Kombination von Druckänderungen mit Temperaturschwankungen, um das Verhalten von Materialien unter extremen Bedingungen zu testen.
- Feuchtigkeits- und Drucktests: Bewertung der Auswirkungen von Feuchtigkeit in Kombination mit Druckänderungen.
- Validierung von Vakuumverpackungen: Bewertung der Integrität von Vakuumverpackungen unter Transport- und Lagerbedingungen.
- Raumfahrtsimulation: Testen von Materialien und Systemen unter extremen Vakuumbedingungen, wie sie im Weltraum herrschen.
Wiederholtes Anwenden von Druck und Vakuum, um die Haltbarkeit eines Produkts oder Systems zu bewerten.
Normen
ASTM D6653
- Niederdrucktests für Transportverpackungen, die auf die Simulation von Höhen- und Druckbedingungen während des Lufttransports abzielen.
ASTM F2096
- Testmethode zur Erkennung von Mikrolecks in flexiblen Verpackungen mithilfe einer Vakuumkammer.
ISO 16495
- Testmethoden für Transportverpackungen mit Fokus auf die Simulation von Druckunterschieden während des Lufttransports.
IEC 60068-2-13
- Testen von Elektronik bei niedrigem Luftdruck zur Simulation der Leistung in großen Höhen oder unter Vakuumbedingungen.
ISO 80369
- Spezifikationen für medizinische Verbindungsstücke, einschließlich Vakuumtests zur Erkennung von Leckagen und zur Sicherstellung der Integrität.
ASTM E493
- Standard-Testmethode zur Bewertung von Geräten unter Vakuumbedingungen.
ASTM F88
- Testmethode zur Messung der Festigkeit von Verpackungsschweißnähten unter Vakuumbedingungen.
RTCA DO-160 (Abschnitt 4)
- Testmethode für Luftfahrtausrüstung, einschließlich Simulation von niedrigem Druck zur Bewertung der Leistung in großer Höhe.
MIL-STD-810, Method 500
- Niederdrucktests (Höhensimulation) für militärische Geräte. Häufig verwendet für Elektronik und Verpackungen, die Druckänderungen ausgesetzt sind.
ISO 2685
- Umgang mit extremen Temperaturen und Vakuumbedingungen für Luftfahrtmaterialien.
ISO 11607
- Testmethoden für sterile Barriereverpackungen für medizinische Geräte, einschließlich Vakuumtests zur Leckerkennung und Integritätserhaltung.
ASTM F1140
- Testmethode zur Messung der Druckfestigkeit von Verpackungen unter Vakuum- oder Überdruckbedingungen.
ISTA Series 3A/3B/3E
- Transporttests, einschließlich Simulation von niedrigem Luftdruck (Vakuum), um die Integrität von Transportverpackungen zu gewährleisten.
Was ist ein Vakuumtest?
Ein Vakuumtest simuliert Umgebungen mit niedrigem Luftdruck, ähnlich den Bedingungen in großen Höhen oder in abgeschlossenen Transportumgebungen wie Frachtflugzeugen.
Auf diese Weise kann Sebert Schwingungstechnik beurteilen, ob Produkte den Druckunterschieden standhalten, die während des Transports oder der Lagerung auftreten können. Die Tests können auch dabei helfen, Lecks in Verpackungen oder Gehäusen von elektronischen und medizinischen Geräten aufzuspüren.
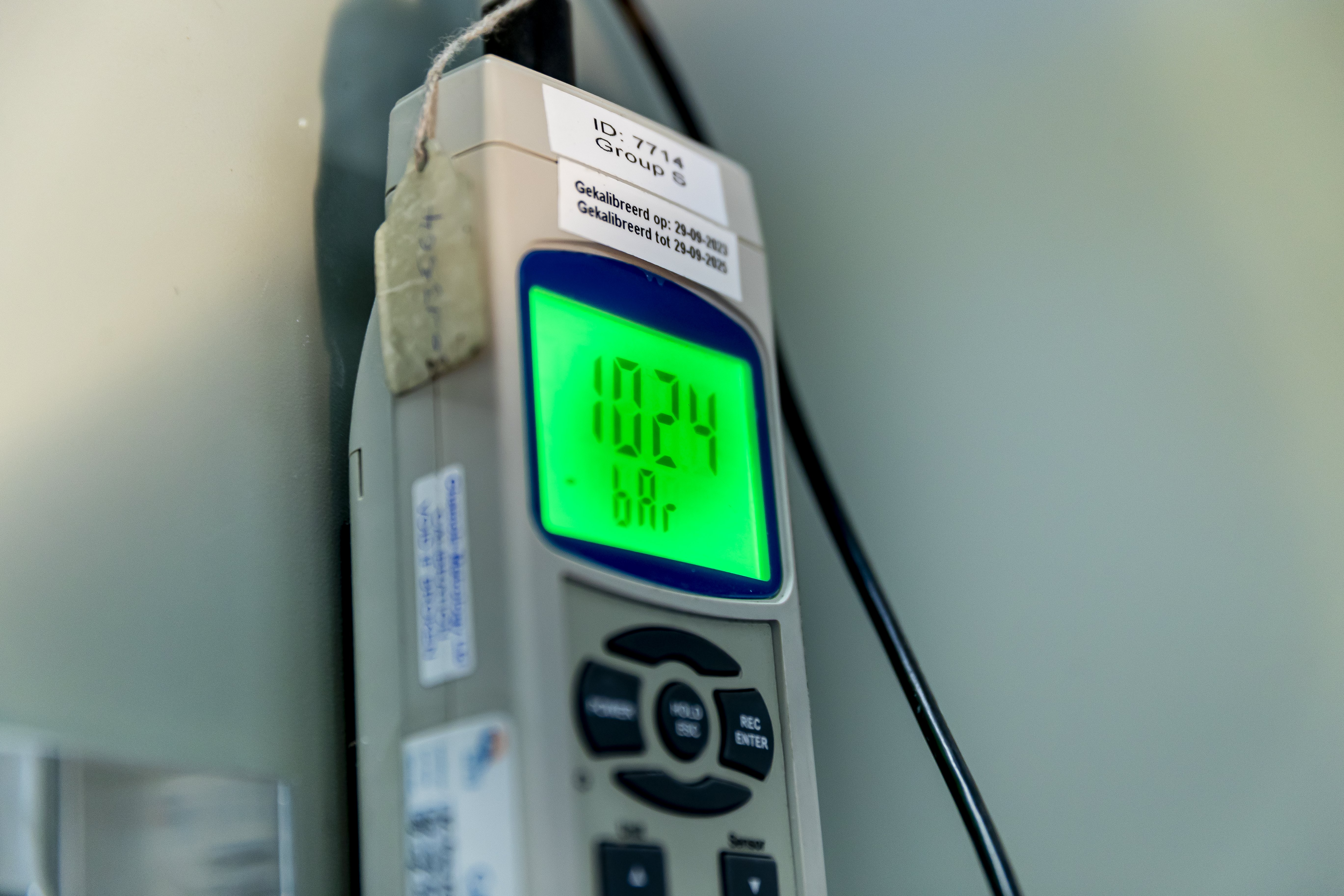
Spezifikationen der Prüfmaschine in unserem Maschinenpark
Mit unserer Vakuumtest-Druckkammer können wir einen Unterdruck simulieren, kombiniert mit Temperatur und Vibrationen. Durch die Ausdehnung des Produkts verliert es seine ursprüngliche Form, und in Kombination mit Temperatur und Vibrationen kann Abrieb (Schleifschäden) auftreten. Dadurch wird das Material an bestimmten Stellen porös, und es entstehen Mikrorisse im Material, die zu Leckagen führen.
Spezifikation:
- Abmessungen: rund 80 cm x Höhe 120 cm
- Unterdruck: 50 - 1000 mbar
- Maximales Gewicht: 1.300 kg
- Temperaturbereich: -40 bis 70 Grad Celsius
Die wichtigsten Gründe, Vakuumtests durchzuführen:
- Lufttransport: Im Laderaum von Flugzeugen kann der Luftdruck auf etwa 595 mbar absinken, was einen signifikanten Druckunterschied im Vergleich zum normalen atmosphärischen Druck (~1013 mbar) verursacht.
- Gebirgstransport: Während des Transports in bergigen Regionen kann der Luftdruck auf bis zu 800 mbar sinken, was ebenfalls luftdichte Verpackungen beeinflussen kann.
- Raumanwendungen: Für Produkte, die unter extremen Bedingungen wie in der Raumfahrt eingesetzt werden, sind Vakuumtests unerlässlich, um ihr Verhalten bei sehr niedrigem Druck zu bewerten.
- Luftdichte Verpackungen:
- Vakuumtests helfen zu beurteilen, ob luftdichte Verpackungen wie versiegelte Beutel, Container oder medizinische Verpackungen Druckunterschieden standhalten können.
- Bei Druckunterschieden können Versiegelungen versagen, wodurch der Inhalt Luft, Feuchtigkeit oder Verunreinigungen ausgesetzt wird.
- Lebensmittel und pharmazeutische Produkte:
- Diese Tests stellen sicher, dass Verpackungen ihre Barriereeigenschaften während des Transports beibehalten, sodass der Inhalt frisch oder steril bleibt.
- Empfindliche Geräte:
- Elektronische Geräte, medizinische Instrumente und andere empfindliche Produkte können durch Druckunterschiede beschädigt werden. Vakuumtests stellen sicher, dass diese Produkte zuverlässig bleiben.
- Materialien mit inneren Luftkammern:
- Produkte wie Kunststoffteile, Stoßdämpfer oder andere Materialien mit Luftkammern können unter niedrigem Druck reißen, sich verformen oder versagen. Vakuumtests identifizieren solche Schwachstellen.
- Vorhersage von Schäden:
- Durch Vakuumtests können potenzielle Probleme wie Lecks, Risse oder strukturelle Schwächen frühzeitig erkannt werden.
- Reduzierung der Transportkosten:
- Durch die Optimierung von Verpackungen und Produkten wird Transportschaden minimiert, was zu geringeren Kosten und weniger Produktverlust führt.
- Elektronik: Bewertung von luftdichten Gehäusen und Schutz interner Komponenten.
- Pharmazeutische und medizinische Verpackungen: Überprüfung steriler Versiegelungen und Barriereeigenschaften.
- Automobil- und Luftfahrtindustrie: Testen von Bauteilen, die wechselnden Druckbedingungen wie Höhenlagen ausgesetzt sind.
- Verpackungsindustrie: Validierung von Versiegelungen und Verpackungsdesigns.
Do you have any questions?
Want to learn more about our testing methods or specific tests? Our experts are here to help with any inquiries you might have. Reach out today and find out how the Sebert Group can support you in delivering unmatched quality and reliability.
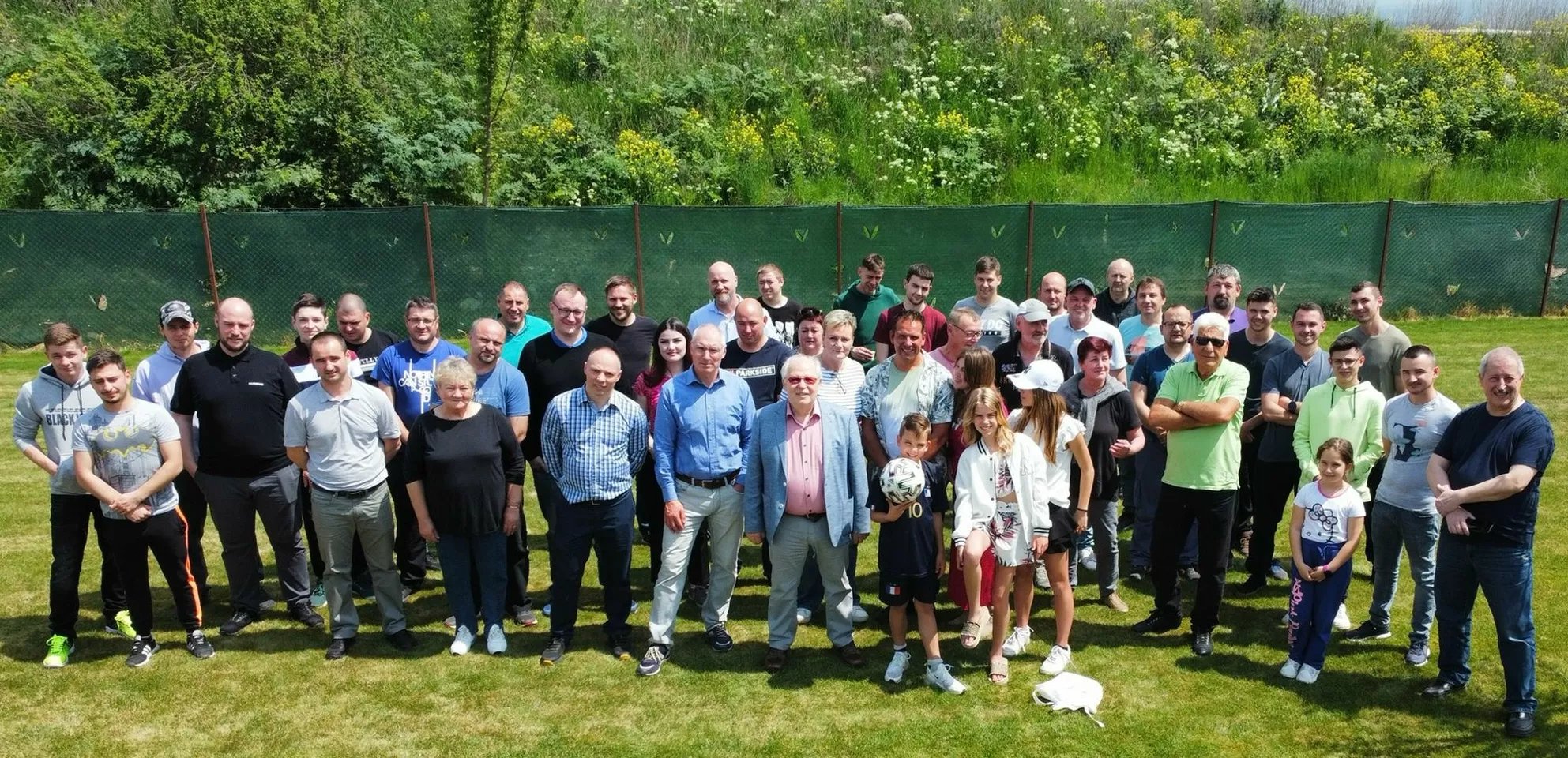