Schock-, Stoß- und Schlagprüfung
Impact durch Fallen, Stoßen oder Kollisionen während des Logistikprozesses und der Lebensdauer eines Produkts ist normal. Stöße können das Produkt mit oder ohne seine Verpackung erheblich beschädigen. Mit einem elektrischen dynamischen Shaketisch, einer Stoßbank, einem schrägen Tester und einer HIT-Maschine kann die Stoßfestigkeit eines Produkts oder einer Verpackung festgestellt werden.
Die kontrollierte Durchführung eines Impact-Tests mit bekannten Stoßniveaus ist entscheidend, um Schwachstellen in einem Produkt oder einer Verpackung zu identifizieren. Anhand der Ergebnisse kann das Produkt oder die Verpackung optimiert werden.
Navigieren Sie zu:
→ Testübersicht
→ Maschinenspezifikationen testen
→ Normen und Standards
→ Gründe zum Testen
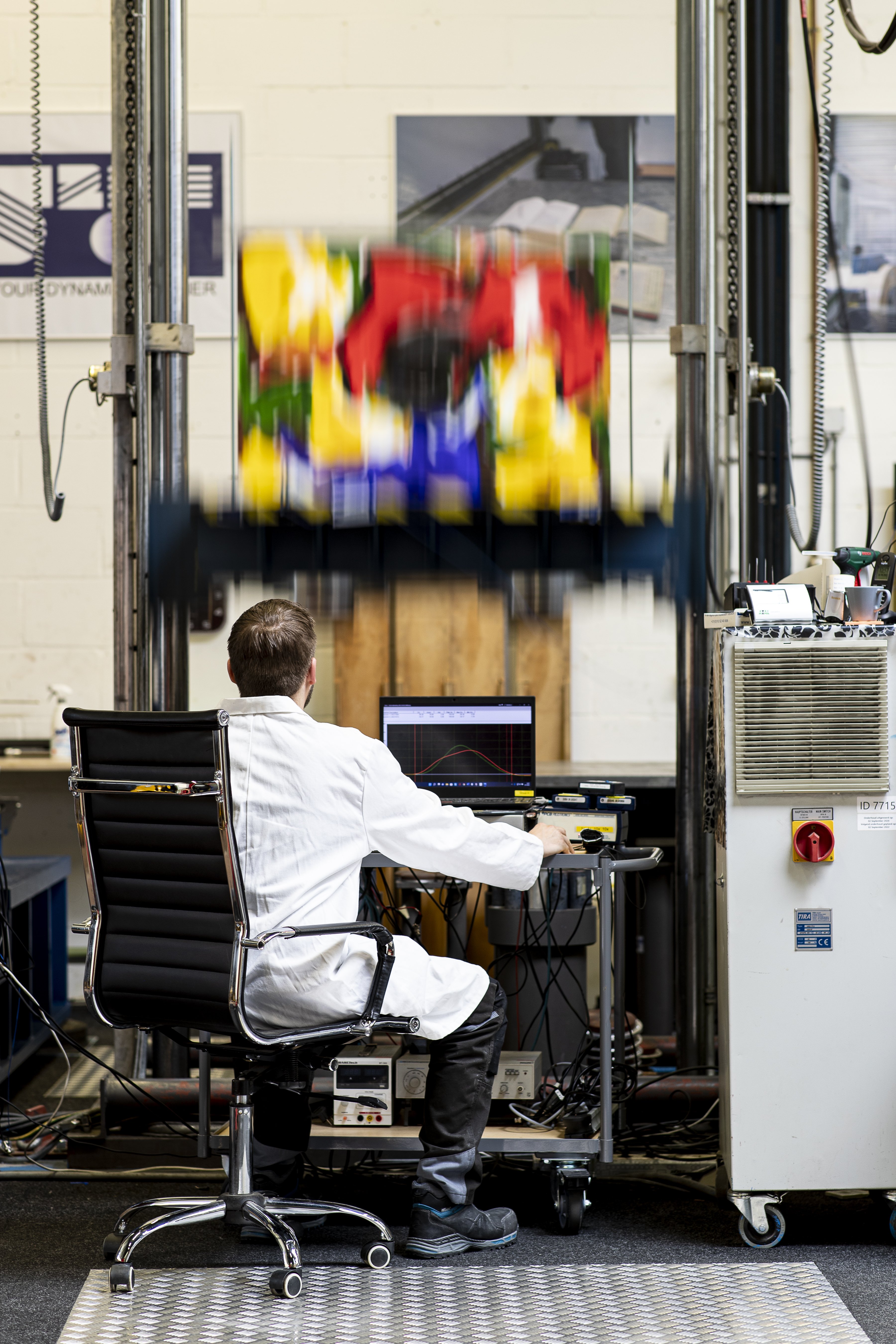
Die verschiedenen Arten von Tests
Eine Übersicht über Schock-/Schlagprüfungen, die die Sebert Group für Sie durchführt:
Schocktests simulieren plötzliche und intensive Kräfte, die beispielsweise durch Stürze, Kollisionen oder abrupte Bewegungen auftreten. Diese Tests sind entscheidend, um die strukturelle Integrität und Funktionalität eines Produkts zu bewerten.
Anwendungsbereiche:
- Prüfung elektronischer Komponenten, wie Leiterplatten, auf ihre Widerstandsfähigkeit.
- Bewertung von Industrieanlagen oder Maschinen, die in betrieblichen Umgebungen Stößen ausgesetzt sind.
- Simulation von Stößen während des Transports, z. B. das Herabfallen einer Kiste von einer Laderampe.
Ausstattung:
- Schockbank: Führt kontrollierte Schockimpulse mit voreingestellten Beschleunigungen und Geschwindigkeiten aus.
Parameter:
- Schockwelle: Form und Dauer des Schocks, z. B. Halbsinus, Rechteck oder Sägezahn.
- Spitzenbeschleunigung (g): Maximale Beschleunigung während des Schocks.
- Dauer: Dauer des Schocks, oft gemessen in Millisekunden.
Aufpralltests konzentrieren sich auf die Kraft einer direkten Kollision oder eines Schlages auf ein Produkt oder eine Verpackung. Diese Tests werden verwendet, um die Widerstandsfähigkeit gegen mechanische Belastung zu messen.
Anwendungsbereiche:
- Bewertung von Verpackungsmaterialien wie Karton, Schaumstoff oder Kunststoff.
- Prüfung empfindlicher Güter wie Glaswaren, Keramik und Elektronik.
- Simulation von Kollisionen zwischen Produkten oder mit externen Objekten während des Transports.
Ausstattung:
- Schiefe-Ebene-Tester: Lässt ein Produkt eine geneigte Fläche hinunterrollen, um Kollisionen zu simulieren.
- Pendelaufpralltester: Verwendet ein Pendel, um eine kontrollierte Kollision zu erzeugen.
Parameter:
- Aufprallgeschwindigkeit: Wird basierend auf der Höhe oder der Aufprallkraft berechnet.
- Aufprallenergie (Joule): Die Energiemenge, die bei der Kollision freigesetzt wird.
Bump-Tests simulieren wiederholte, weniger intensive Stöße, die beispielsweise durch den Transport auf unebenen Straßen oder Vibrationen in Fahrzeugen entstehen. Ziel ist es, Ermüdungsschäden und Materialermüdung zu identifizieren.
Anwendungsbereiche:
- Prüfung von Produkten, die häufig wiederholten Vibrationen ausgesetzt sind, wie Fahrzeuge, Container und Haushaltsgeräte.
- Bewertung von Verpackungen hinsichtlich ihrer Fähigkeit, Stöße über einen längeren Zeitraum zu absorbieren.
Ausstattung:
- Bump-Tester: Eine Maschine, die ein Produkt wiederholt mit kontrollierter Kraft „springen“ lässt.
- Vibrationstisch: Kombiniert Bump-Tests mit Vibrationen für realistischere Simulationen.
Parameter:
- Anzahl der Zyklen: Wie oft das Produkt einem Stoß ausgesetzt wird.
- Höhe des Stoßes: Die vertikale Distanz, die ein Produkt bei jedem Stoß zurücklegt.
Diese Tests simulieren den horizontalen Aufprall von Verpackungen, die auf ein Hindernis treffen (z. B. wenn ein Gabelstapler mit voller Geschwindigkeit gegen eine andere Palette stößt). Dieser Testtyp wird für Szenarien verwendet, in denen sich Produkte in einem Fahrzeug oder Lager bewegen.
Anwendungsbereiche:
- Prüfung des Rollwiderstands und der Aufprallbeständigkeit.
- Bewertung von Verpackungen hinsichtlich Kollisionen beim Transport auf schrägen Flächen.
Ausstattung:
- Horizontaler Aufpralltester: Lässt Produkte kontrolliert mit variabler Geschwindigkeit rollen und aufprallen.
Normen
ASTM D5276:
Standard-Testmethode für den Falltest beladener Behälter
- Beschreibung: Verfahren zur Durchführung von Falltests an vollständig beladenen Verpackungen.
- Anwendung: Prüfung der Fallbeständigkeit und Schutzwirkung während des Transports.
ASTM D880:
Standard-Testmethode für Aufpralltests von Versandbehältern
- Beschreibung: Richtlinien für Aufpralltests an Verpackungen, einschließlich Kollisionen und Schlagkräften.
- Anwendung: Bewertung der Integrität von Verpackungen.
ASTM D3332:
Standard-Testmethode für die mechanische Stoßempfindlichkeit von Produkten
- Beschreibung: Tests der Empfindlichkeit von Produkten und Komponenten gegenüber mechanischen Stößen.
- Anwendung: Prüfung empfindlicher Produkte wie Elektronik.
ASTM D6179:
Standard-Testmethoden für die grobe Handhabung von gebündelten Lasten
- Beschreibung: Methoden zur Simulation der groben Behandlung von Produkten, wie Stürze und Kollisionen.
- Anwendung: Prüfung schwerer und zusammengesetzter Lasten.
MIL-STD-810:
Umwelttechnische Anforderungen und Labortests
- Beschreibung: Umfasst Testverfahren für Stöße, Vibrationen und Aufpralle unter extremen Bedingungen.
- Anwendung: Häufig verwendet für militärische und Luftfahrtprodukte.
MIL-STD-202:
Standard-Testmethoden für elektronische und elektrische Bauteile
- Beschreibung: Enthält Methoden zur Prüfung der Stoßfestigkeit elektronischer Bauteile.
- Anwendung: Prüfung von Leiterplatten, Steckverbindern und anderer empfindlicher Ausrüstung.
AECTP 400:
Mechanischer Stoßtest
- Beschreibung: Teil der Allied Environmental Conditions and Test Procedures (AECTP), bietet Richtlinien zur Prüfung der mechanischen Stoßbeständigkeit von Systemen, Komponenten und Verpackungen.
- Anwendung:
- Militärische Systeme: Prüfung der Stoßfestigkeit von Waffensystemen, Fahrzeugen und militärischer Elektronik.
- Luft- und Raumfahrt: Bewertung der Stoßbeständigkeit empfindlicher Komponenten bei Starts oder Landungen.
- Transport und Logistik: Beurteilung der Haltbarkeit von Produkten und Verpackungen bei grober Handhabung.
- Industrielle Anwendungen: Prüfung von Geräten, die starken Aufprallkräften in rauen Arbeitsumgebungen ausgesetzt sind.
ISTA 1A:
Nicht-simulierender Integritätstest
- Beschreibung: Basistest zur Simulation von Stößen und Vibrationen während des Transports.
- Anwendung: Geeignet zur Bewertung einfacher Transportverpackungen.
ISTA 3A:
Verpackte Produkte für den Versand über Paketdienstleister
- Beschreibung: Spezifische Richtlinien für Stoß- und Aufpralltests von Paketen, die per Kurier verschickt werden.
- Anwendung: Prüfung von Paketen bis 70 kg für E-Commerce und Distribution.
ISTA 6-Amazon.com:
- Beschreibung: In Zusammenarbeit mit Amazon entwickelte Tests zur Prüfung von Verpackungen für deren Distributionssysteme.
- Anwendung: Verpackungsvalidierung für den Onlinehandel.
ISO 2248:
- Verpackung – Vollständige, gefüllte Transportverpackungen – Vertikaler Aufpralltest
- Beschreibung: Richtlinien für Tests von vertikalen Aufprallen auf vollständig gefüllte Transportverpackungen.
- Anwendung: Bewertung von Verpackungen bei Lagerung und Transport, wie Stürze und Stöße.
ISO 8318:
- Verpackung – Vollständige, gefüllte Transportverpackungen – Sinusförmiger Vibrationstest
- Beschreibung: Richtlinien zur Simulation von Vibrationen und wiederholten Stößen während des Transports.
- Anwendung: Prüfung der Widerstandsfähigkeit von Verpackungen gegen Stoßeinwirkung durch Vibrationen.
ISO 2244:
- Verpackung – Vollständige, gefüllte Transportverpackungen – Horizontaler Aufpralltest
- Beschreibung: Richtlinien für Tests horizontaler Aufpralle, z. B. Kollisionen in LKWs oder Lagern.
- Anwendung: Prüfung seitlicher Kräfte auf Verpackungen.
EN 15552:
Packaging – Transport packages – Drop test
- Beschrijving: Procedures voor het uitvoeren van valtesten volgens Europese richtlijnen.
- Toepassing: Beoordeling van verpakkingen in logistieke ketens.
EN 12642:
Load Securing on Road Vehicles
- Beschrijving: Richtlijnen voor het beveiligen van ladingen tijdens transport.
- Toepassing: Testen van de stabiliteit van ladingen in vrachtwagens en containers.
Akkreditierung:
Sebert Group: Zuverlässige und weltweite Anerkennung
Sebert Trillingstechniek ist von dem Raad voor Accreditatie (RvA), einem Teil der European Accreditation (EA) und ILAC, akkreditiert. Tests in unserem ISO 17025-akkreditierten Labor werden weltweit anerkannt, im Gegensatz zu ISO 9001- oder ISTA-Laboren.
ISO/IEC 17025 erfordert qualifiziertes Personal, kalibrierte Ausrüstung und validierte Methoden. Dies garantiert unabhängige und zuverlässige Testergebnisse von hoher Qualität. Unser Geltungsbereich ist auf der RvA-Website zu finden (Registrierungsnummer L540).
Vorteile des ILAC•MRA-Logos
Das ILAC•MRA-Logo auf den Berichten garantiert eine weltweite Akzeptanz, einschließlich der EU, USA, Japan und mehr.
Es vermeidet doppelte Tests und Bürokratie und unterstützt das Prinzip des freien Handels: "Ein getestetes Produkt wird überall akzeptiert."
Akkreditiertes Prüfbericht für Schock-, Bump- und Impacttests
Möchten Sie einen akkreditierten bericht für schock-, bump- und aufpralltests? Dann müssen die tests im folgenden umfang durchgeführt werden:
- Testtyp: Halbsinusförmiger Stoß/Stoß
- Bedingungen: Kalibriert und geprüft
- Spezifikationen:
- Maximale Beschleunigung: 11.500 m/s²
- Nominelle Dauer: 1 - 65 ms
- Maximale Spitze-zu-Spitze-Geschwindigkeit: 13 m/s
- Testtyp: Blockförmiger Stoß/Stoß
- Bedingungen: Kalibriert und geprüft
- Spezifikationen:
- Maximale Beschleunigung: 4.000 m/s²
- Nominelle Dauer: 4 - 65 ms
- Maximale Spitze-zu-Spitze-Geschwindigkeit: 7,6 m/s
- Testtyp: Sägezahn – Schock/Stoß
- Bedingungen: Kalibriert und geprüft
- Spezifikationen:
- Maximale Beschleunigung: 3.000 m/s²
- Nenndauer: 4 - 40 ms
- Maximale Spitze-zu-Spitze-Geschwindigkeit: 4,6 m/s
- Testtyp: Auswirkung
- Bedingungen: Kalibriert und geprüft
- Spezifikationen:
- Maximales Gewicht: 2000 kg
- Maximale Geschwindigkeit: 4 m/s
Schock-, Bump- und Aufpralltests
Es gibt verschiedene Arten von Tests, die verwendet werden, um die Leistung von Produkten unter unterschiedlichen Bedingungen zu bewerten. Die häufigsten Szenarien von Schock-, Bump- oder Aufprallsituationen können wir realistisch nachbilden!
Jede Testart wird je nach den gestellten Anforderungen und dem Ziel des Tests angewendet. Mit diesen präzisen und zuverlässigen Testmethoden erfüllt Ihr Bericht die höchsten Standards und wird weltweit anerkannt.
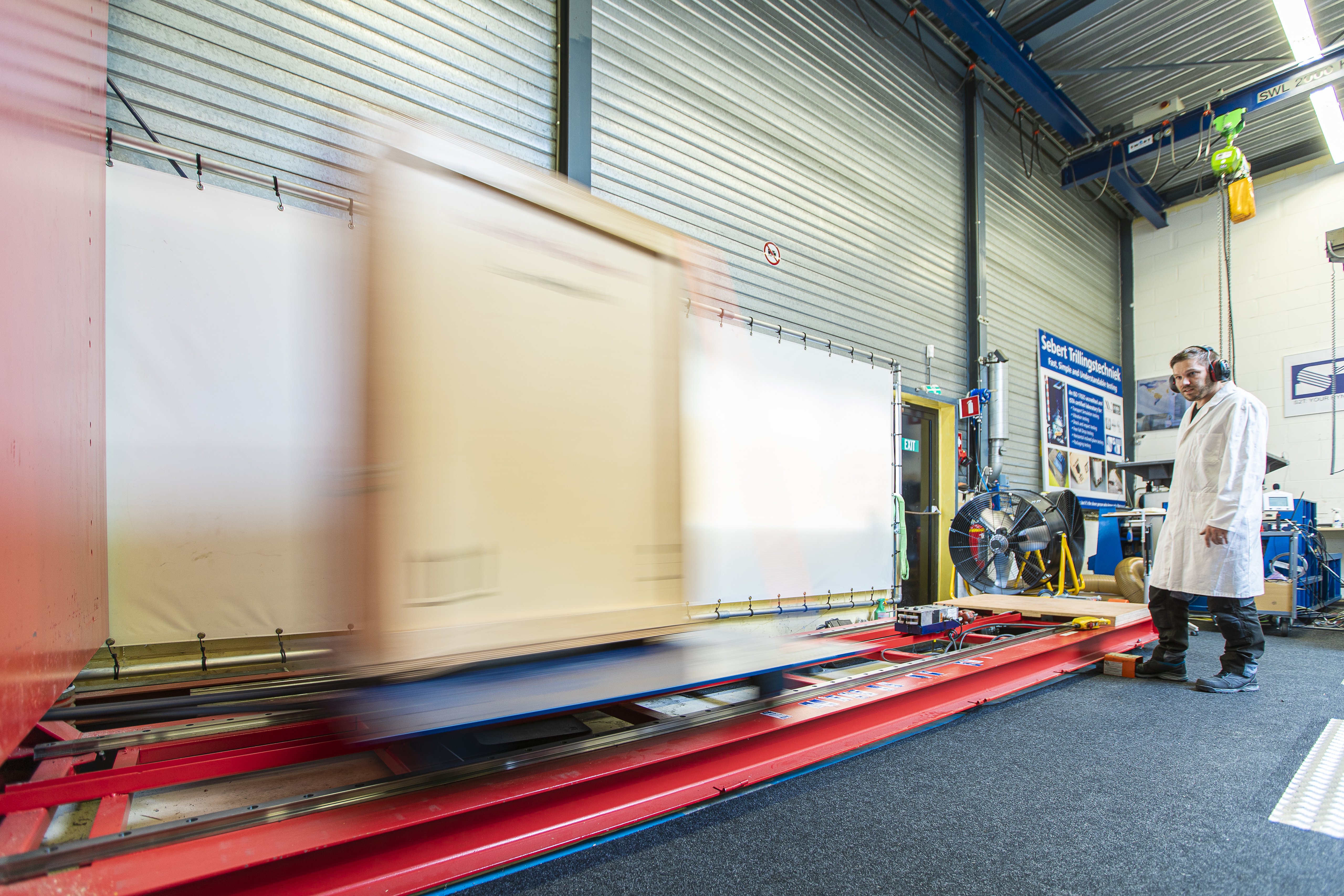
Spezifikationen der Prüfmaschinen in unserem Maschinenpark
Durch den Einsatz dieser fortschrittlichen Technologie ist es möglich, einen Stoß- und Impact-Test auf einem unserer Shaketische gemäß der MIL STD 810 und IEC 60068-2-27 durchzuführen. Der Impact kann sowohl vertikal als auch horizontal simuliert werden. Zudem ist es möglich, ein SRS (Stoßantwortspektrum) anzubieten.
Spezifikationen:
- Testgewicht max.: 700 kg
- Testrichtung: vertikal und horizontal
- Tischabmessungen: 1200 x 1200 mm
- Spitzenbeschleunigung: 100 g
- Geschwindigkeit: 2,5 m/s
- Verlagerung: 60 mm (Spitze-Spitze)
Die Norm ASTM D3332 beschreibt zum Beispiel den „Step Velocity and Step Acceleration Test“ zur Bestimmung der sogenannten „Damage Boundary Curve“ (D-Bound-Kurve). Diese Kurve gibt an, bei welchen kritischen Beschleunigungen und Geschwindigkeitsänderungen das Produkt keinen Schaden durch einen Stoß oder Fall erleidet. Mit dieser Schockbank können verschiedene Halb-Sinus-, Block- und Sägezahnimpulse erzeugt werden.
Spezifikationen:
- Testgewicht max.: 1.200 kg
- Testrichtung: vertikal
- Tischabmessungen: 1200 x 1200 mm
- Spitzenbeschleunigung: 1.200 g
- Geschwindigkeit: 6 m/s (bis zu 10 m/s aufrüstbar)
- Verlagerung: 2.000 mm
Unter anderem beschreiben ASTM D 5277 und ISO 2244 einen horizontalen Impacttest, bei dem eine Palette mit einer bestimmten Geschwindigkeit gegen eine 13 mm dicke Stahlwand prallt. Diese Simulation gibt Aufschluss über die Stabilität der Palette während des Transports. Angenommen, ein Lkw bremst stark (<0,8 g), dann ist es von Vorteil, wenn Ihre Palette noch aufrecht steht.
Spezifikationen:
- Testgewicht: 2.000 kg
- Testrichtung: horizontal (unter einem Winkel von 10 Grad)
- Tischabmessungen: 1500 x 1500 mm
- Geschwindigkeit: 4 m/s
ASTM D 4003 und verschiedene ISTA-Verfahren beschreiben einen horizontalen Schocktest, bei dem eine Palette einen Impuls von fünfzehn Millisekunden und eine Geschwindigkeit von 0,9 Metern pro Sekunde überstehen muss.
Spezifikationen:
- Testgewicht: 2.000 kg
- Testrichtung: horizontal
- Tischabmessungen: 1500 x 1500 mm
- Geschwindigkeit: 2 m/s
- Impulsdauer: Datenakquisition
Durchführung von Schock-, Bump- und Aufpralltests: Wichtige Gründe:
Während des Transports und der Lebensdauer eines Produkts kann es zu Stößen durch Stürze, Erschütterungen oder Kollisionen kommen. Durch die Simulation dieser Bedingungen kann festgestellt werden, wie gut das Produkt oder die Verpackung diesen Einflüssen standhält.
Stöße können erhebliche physische und funktionale Schäden an einem Produkt verursachen. Mit Schocktests kann überprüft werden, ob das Produkt in der Lage ist, die Einwirkungen zu überstehen, ohne Defekte aufzuweisen.
Eine Verpackung muss nicht nur ästhetisch, sondern vor allem funktional sein. Tests helfen dabei, Schwachstellen in der Verpackung zu identifizieren, sodass sie verbessert werden kann, um das Produkt besser zu schützen.
Durch die frühzeitige Erkennung von Schwachstellen können Unternehmen kostspielige Reparaturen, Ersatzlieferungen und Kundenbeschwerden vermeiden. Dies führt zu einem effizienteren Ressourceneinsatz und langfristig niedrigeren Kosten.
Viele Branchen haben spezifische Normen und Anforderungen an die Schockfestigkeit (z.B. ISTA, ASTM, ISO). Schocktests stellen sicher, dass Produkte und Verpackungen diesen internationalen Qualitätsstandards entsprechen.
Mit Werkzeugen wie einem elektrischen dynamischen Schwingtisch, einer Schockbank, einem Inclined Plane Tester und einer HIT-Maschine kann präzise festgestellt werden, wie ein Produkt oder eine Verpackung auf unterschiedliche Schockniveaus reagiert. Diese kontrollierte Umgebung macht die Testergebnisse zuverlässig und reproduzierbar.
Die Ergebnisse von Schocktests liefern wertvolle Erkenntnisse, mit denen Produkte und Verpackungen verbessert werden können. Dies fördert Innovation und die Entwicklung nachhaltigerer und robusterer Designs.
Rotation des Produkts innerhalb eines kubischen Rahmens, um Schlagprüfungen in alle Richtungen auf einem vertikalen Stoßtisch zu ermöglichen.

Do you have any questions?
Want to learn more about our testing methods or specific tests? Our experts are here to help with any inquiries you might have. Reach out today and find out how the Sebert Group can support you in delivering unmatched quality and reliability.
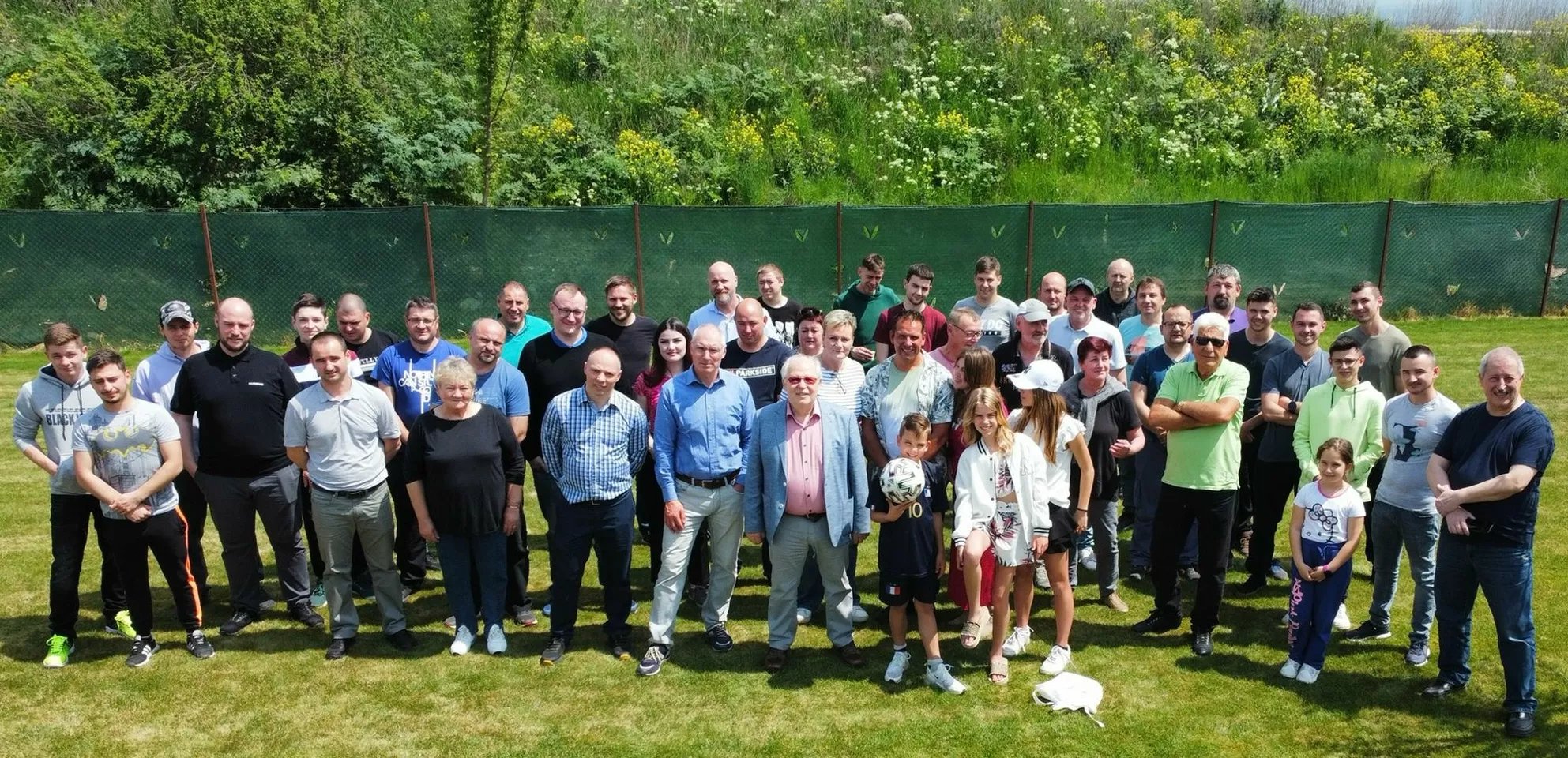