Salzsprühnebeltest
Der Salzsprühnebeltest ist ein standardisiertes Verfahren zur Bewertung der Korrosionsbeständigkeit von Materialien, Produkten und Beschichtungen.
Die Prüfung erfolgt in einer kontrollierten Umgebung, in der die Materialien einem Salznebel ausgesetzt werden, der korrosive Bedingungen nachahmt.
Navigieren Sie zu:
→ Testübersicht
→ Maschinenspezifikationen testen
→ Normen
→ Gründe zum Testen
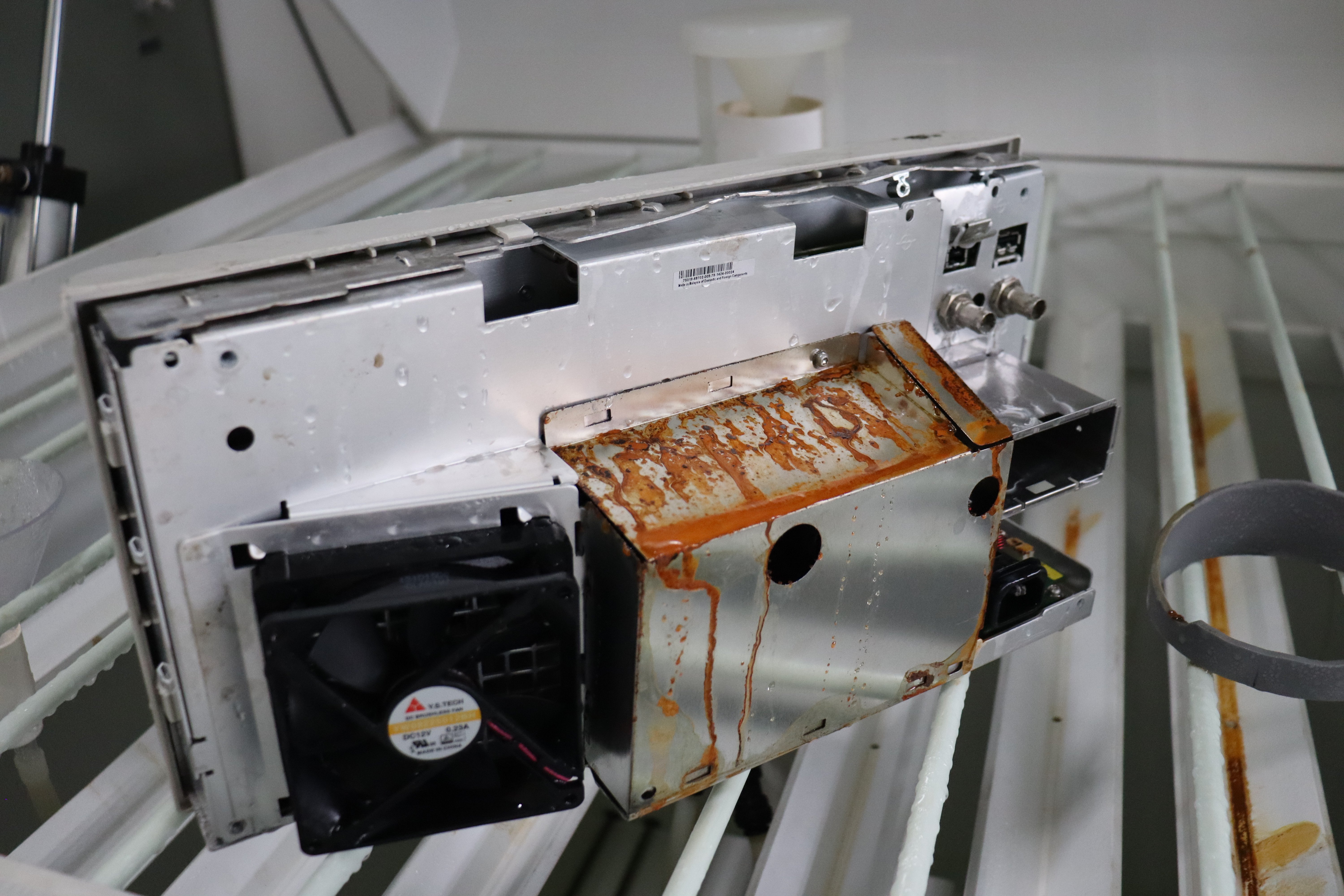
Salzsprühnebeltests
Eine Übersicht der Tests, die die Sebert Group für Sie durchführt:
- Beschreibung: Der am häufigsten verwendete und standardisierte Test. Es wird eine neutrale Salzlösung (pH 6,5-7,2) verwendet, um korrosive Bedingungen zu simulieren.
- Anwendung: Geeignet für allgemeine Korrosionstests von Beschichtungen, Metallen und behandelten Oberflächen.
Normen:
ISO 9227, ASTM B117, IEC 60068-2-11, IEC 60068-2-52
- Beschreibung: Eine Variante des Salzsprühtests, bei der Essigsäure der Salzlösung hinzugefügt wird, was zu einem niedrigeren pH-Wert (pH 3,1-3,3) führt. Dies beschleunigt den Korrosionsprozess.
- Anwendung: Häufig verwendet zur Prüfung von Beschichtungen wie Anodisierung oder organischen Beschichtungen auf Aluminium.
Normen:
ISO 9227
- Beschreibung: Eine noch aggressivere Variante, bei der Kupfer(II)-chlorid der Essigsäurelösung hinzugefügt wird, was zu sehr schneller Korrosion (pH 3,1-3,3) führt.
- Anwendung: Häufig in der Automobil- und Luftfahrtindustrie zur Prüfung von stark korrosionsbeständigen Materialien verwendet.
Normen:
ISO 9227, ASTM G85
- Beschreibung: Kombiniert Salzsprühtests mit trockenen und feuchten Zyklen, um realistischere Umgebungsbedingungen zu simulieren.
- Anwendung: Verwendet für fortgeschrittene Korrosionstests in Branchen wie Schifffahrt, Offshore und Automobilindustrie.
Normen:
ASTM G85, SAE J2334
- Beschreibung: Ein spezifischer zyklischer Test, der Salzsprühen mit Trockenzyklen und einer verdünnteren Salzlösung kombiniert. Er ist weniger korrosiv als NSS, simuliert jedoch realistischere Expositionen.
- Anwendung: Geeignet für Produkte, die langfristig milder Korrosion ausgesetzt sind.
Normen:
ASTM G85 (Anhang A5)
- Beschreibung: Verwendet echtes Meerwasser oder eine synthetische Version von Meerwasser als Salzlösung, um maritime Bedingungen nachzuahmen.
- Anwendung: Eingesetzt für Materialien in Offshore- oder Schiffbauanwendungen.
Normen:
Keine standardisierte internationale Norm, oft kundenspezifisch angepasst.
- Beschreibung: Materialien werden Salzsprühtests unterzogen, kombiniert mit Vibrationen, Stößen oder anderen mechanischen Belastungen.
- Anwendung: Für Anwendungen in anspruchsvollen Umgebungen wie der Automobilindustrie oder bei industriellen Maschinen.
- Beschreibung: Testbedingungen werden an die spezifischen Anforderungen des Kunden angepasst, wie:
- Variable Salzkonzentrationen
- Kombination aus hohen Temperaturen und Salzsprühnebel
- Langzeitprüfungen
- Anwendung: Für Nischenprodukte oder extreme Einsatzbereiche.
Normen
Bewertung der Beständigkeit von Materialien und Bauteilen gegen Korrosion, die durch Salzsprühnebel verursacht wird.
Methode zur Bewertung der Beständigkeit eines Produkts oder Materials gegen Korrosion in einer Salzsprühumgebung.
Diese Norm ermöglicht fortschrittlichere Korrosionstests, einschließlich zyklischer Exposition und der Verwendung zusätzlicher chemischer Substanzen. Sie richtet sich an Situationen, in denen einfache Salzsprühtests wie ASTM B117 nicht ausreichen.
Militärische Testmethode zur Bewertung der Korrosionsbeständigkeit von Materialien und Geräten in Umgebungen, die von Salzsprühnebel und Seeluft beeinflusst werden.
Deutsche Norm, die speziell in der Automobilindustrie verwendet wird, um Salzsprühtests durchzuführen. Diese Testmethodologie wurde vom Verband der Automobilindustrie (VDA) entwickelt und dient zur Bewertung der Korrosionsbeständigkeit von Metallen, Beschichtungen und anderen Materialien, die in Fahrzeugen verwendet werden.
Korrosionstests in künstlichen Atmosphären – Salzsprühtests. Diese Norm wird weltweit verwendet und findet Anwendung in zahlreichen Branchen, darunter Automobil, Luftfahrt, Bauwesen und Schifffahrt.
Corrosiebestendigheid van materialen, coatings en producten te beoordelen door ze bloot te stellen aan een gecontroleerde zoutnevelomgeving. Het is een versnelde test, bedoeld om in een korte tijd een indicatie te geven van hoe goed een materiaal bestand is tegen corrosie in echte omgevingen.
Die Methode simuliert die tägliche Exposition von Fahrzeugen gegenüber natürlichen Wetterbedingungen wie Regen, salzhaltiger Luft, Temperaturschwankungen und Trockenheit. Der Test dient zur Vorhersage der Lebensdauer und Korrosionsbeständigkeit von Materialien und Beschichtungen unter realen Einsatzbedingungen.
Testen realistischerer Szenarien
Der Sebert Group kombiniert den Salzsprühtest möglicherweise mit anderen Umgebungs- und mechanischen Tests, wie Schwingungen oder thermischen Zyklen. Dies bietet ein umfassenderes Bild davon, wie sich ein Produkt unter kombinierten Belastungen verhält.
Diese Tests sind entscheidend für die Verifizierung von Materialien und Produkten, die korrosiven Umgebungen ausgesetzt sind. Sie bieten Einblicke in die Haltbarkeit und Eignung Ihres Produkts für spezifische Anwendungen, wodurch Qualität und Lebensdauer sichergestellt werden.
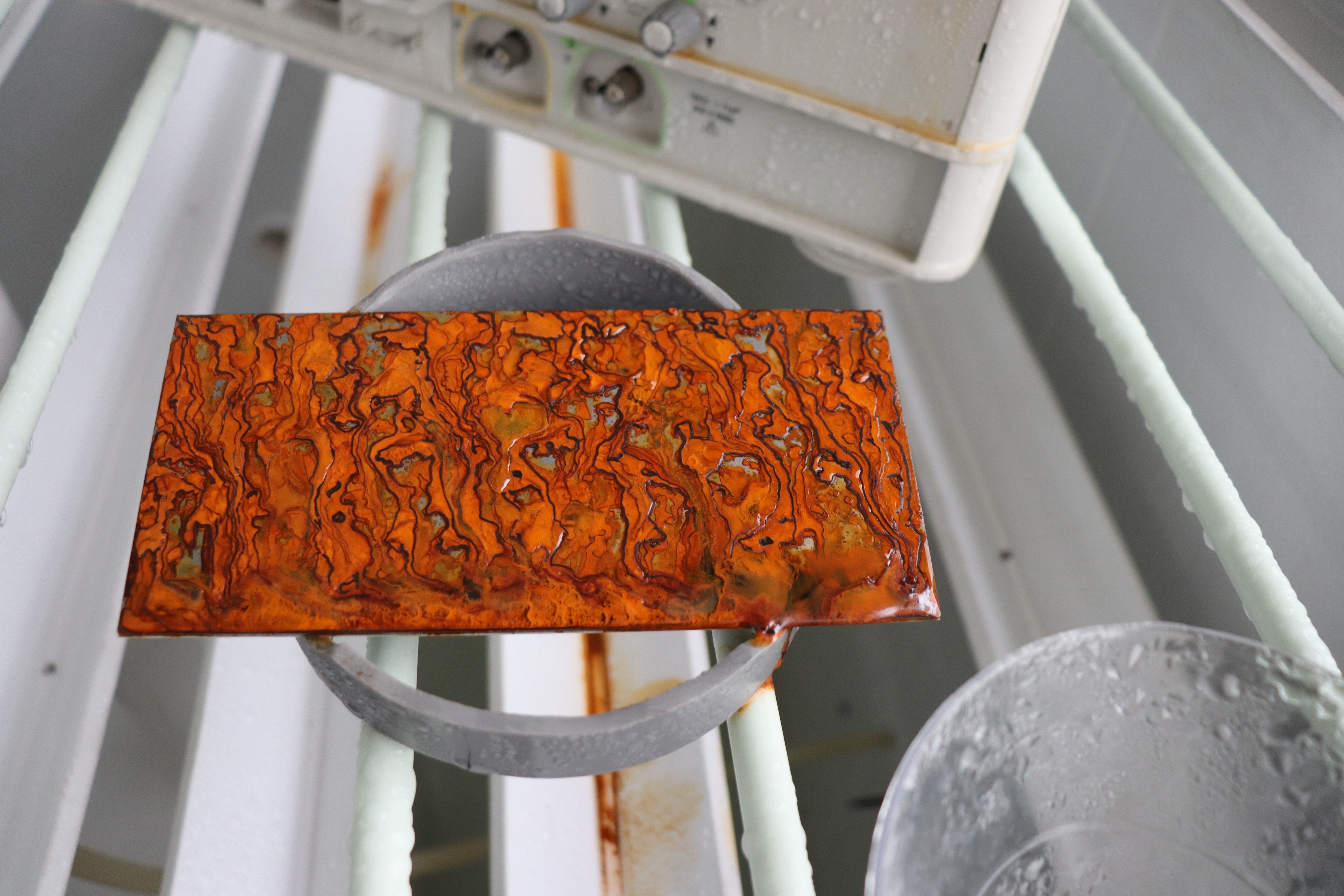
Spezifikationen für Salzsprühtests und Prüfkammern
Die Maschine, die für den Salzsprühtest verwendet wird, ist eine spezialisierte Salzsprühtestkammer (auch Korrosionskammer oder Salt Spray Chamber genannt). Diese Maschine ist so konzipiert, dass sie in einer kontrollierten Umgebung standardisierten Salzsprühnebel erzeugt und aufrechterhält, wodurch Materialien oder Produkte über einen längeren Zeitraum korrosiven Bedingungen ausgesetzt werden können.
Spezifikationen des Salzsprühtests:
- Salzkonzentration: 5 % Salzlösung, bestehend aus 99,5 % reinem NaCl, gemischt mit demineralisiertem Wasser.
- Temperatur: Standardmäßig auf 35 °C (±2 °C) eingestellt, mit einem Bereich von 5 °C bis 55 °C.
- Abmessungen der Testkammern:
- Kleine Testkammer: 450 x 600 x 400 mm
- Große Testkammer: 980 x 990 x 550 mm
Die Durchführung eines Salzsprühtests kann aus folgenden Gründen entscheidend sein:
- Der Test simuliert eine korrosive Umgebung, die häufig durch salzhaltige Luft oder Wasser verursacht wird, wie in Küstenregionen oder bei winterlichen Bedingungen (z. B. Streusalz).
- Er bewertet, wie gut ein Material, eine Beschichtung oder ein Produkt gegen Korrosion und Oxidation beständig ist.
- Der Salzsprühtest wird häufig verwendet, um zu überprüfen, ob ein Material die Anforderungen und Spezifikationen in Bezug auf Haltbarkeit und Zuverlässigkeit erfüllt.
- Dies ist besonders wichtig in Branchen wie der Automobilindustrie, Luftfahrt, Schifffahrt und Bauwesen, wo Korrosionsschutz von entscheidender Bedeutung ist.
- Er unterstützt Hersteller und Ingenieure bei der Auswahl der geeignetsten Korrosionsschutzbehandlungen, wie Galvanisierung, Pulverbeschichtung oder Anodisierung.
- Der Test liefert zudem Einblicke in die Leistung verschiedener Beschichtungen unter vergleichbaren Bedingungen.
- Der Test reproduziert Bedingungen, die in einer natürlichen Umgebung Jahre dauern würden, und beschleunigt so den Prozess der Produktentwicklung und -validierung.
- Dies ist besonders nützlich für Anwendungen, bei denen Produkte extremen Bedingungen ausgesetzt sind, wie Offshore-Anlagen oder industrielle Umgebungen.
- Der Sebert Group kombiniert den Salzsprühtest möglicherweise mit anderen Umgebungs- und mechanischen Tests, wie Schwingungen oder thermischen Zyklen. Dies bietet ein umfassenderes Bild davon, wie sich ein Produkt unter kombinierten Belastungen verhält.
- Die Durchführung kombinierter Tests stellt sicher, dass Produkte realistischeren Szenarien ausgesetzt werden, wie z. B. Vibrationen in einer korrosiven Umgebung (beispielsweise ein Fahrzeug, das in einer salzreichen Umgebung fährt).
- Diese Tests sind entscheidend für die Verifizierung von Materialien und Produkten, die korrosiven Umgebungen ausgesetzt sind. Sie bieten Einblicke in die Haltbarkeit und Eignung Ihres Produkts für spezifische Anwendungen, wodurch Qualität und Lebensdauer sichergestellt werden.
Do you have any questions?
Want to learn more about our testing methods or specific tests? Our experts are here to help with any inquiries you might have. Reach out today and find out how the Sebert Group can support you in delivering unmatched quality and reliability.
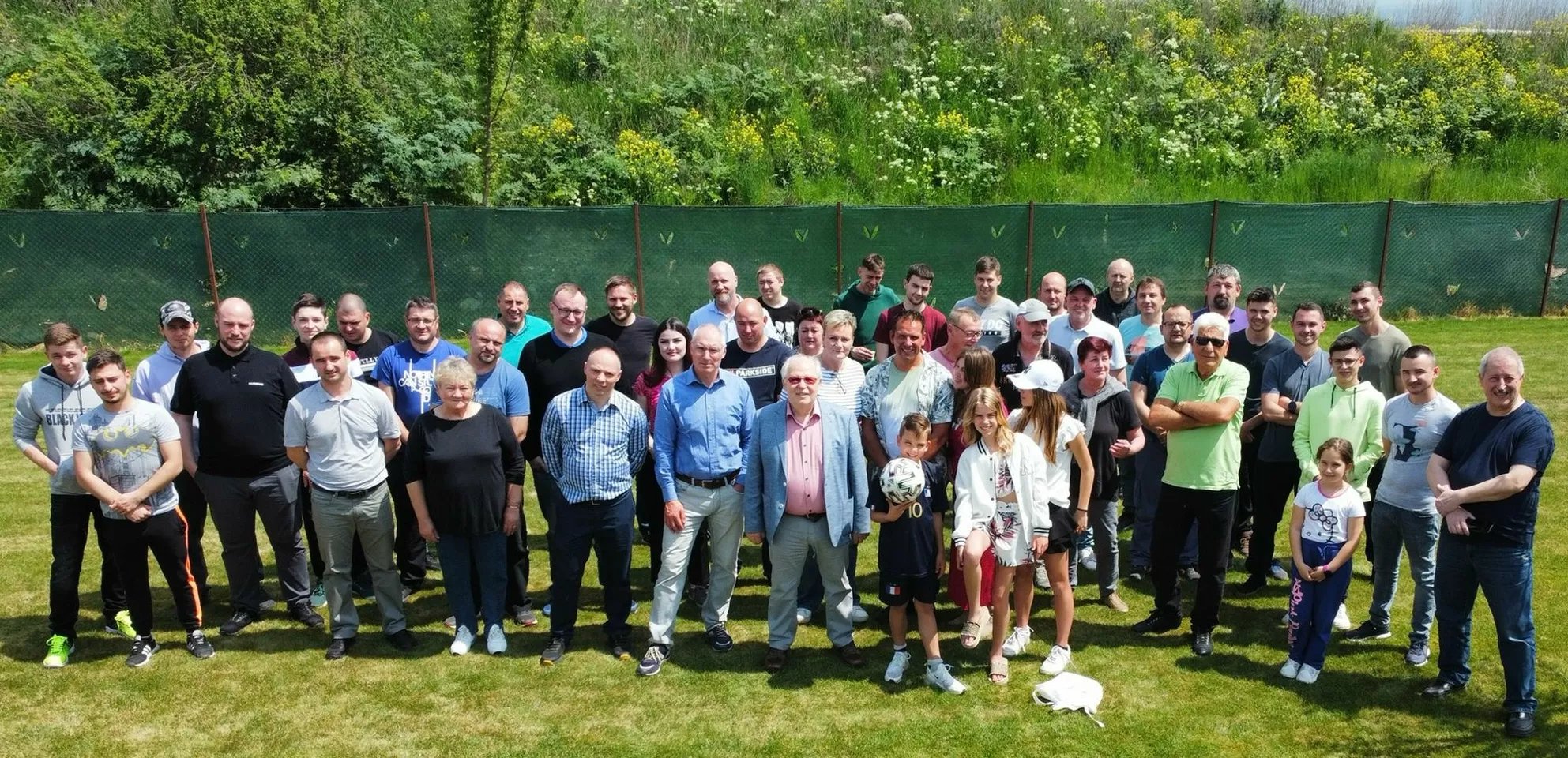